Do you have questions about designing control panels and industrial equipment? Have you always wanted to know the important components of your control panel? Would you like to know the things to look out for in good control panel design? In this guide we examine the most common control panel types, their roles in the manufacturing process and the more important electrical components you should be thinking about while still in the design phase of your panel.
Electrical components need to be organized in a way that optimizes their performance to ensure the best results. If you wanted to control, influence or modify the way your industrial equipment worked or interacted with one another, this is where the control panel comes in. Basically, the control panel provides the ability to change the system settings.
Control panel enclosures come in a variety of shapes and sizes their internal electrical controls purpose is to control the process and provide a single collective base for the operator to control the manufacturing. In other words, a properly designed industrial control panel will allow you to manage the utilities as well as the features of both the hardware and software systems. This is possible because there are a range of control settings that manage the user interface, display, and more. Depending upon the requirements and usage of the system, control panels can be designed as closed-loop, open-loop, or combined (open and closed-loop). All of these have there reason for use, but mostly it depends on the type of feedback needed to keep the system running at optimum levels.
There are numerous types of control panels and each of them contains different components that drive or execute programmed functions. The control panel, in general, manages the peripheral devices and communicates between the host computer and the peripheral devices. Ultimately the software and hardware function together enabling a quick and proper response to running the process with little or no downtime.
Further functions of the control panel are consolidation of all connections and providing power to peripheral devices as needed. Some programmed functions cannot be changed at the control panel, but things that could be done include turning on and off of equipment, motor speed control, control of movement directions, and opening or closing of valves. You can see that your control panel helps you manage many things you would need to configure in your factory or within a piece of equipment. Not only that, but it also allows you to do it with one easy interface. There are a number of control panel types, but we will only take a look at the types that are most frequently employed in industrial manufacturing and automation environments. Maybe this will be just what you need to help get your panel designed, if not you can always contact us for control panel assistance!
Control Panel: Often referred to as a Programmable Logic Controller (PLC) Panels are a common site in an industrial environment or manufacturing facility. These are where industrial computers are kept that connect and monitor input devices and execute programs. Based on the state of the input devices, these PLC panels control the important functions of monitoring and controlling outputs, sounding alarms, open/close valves, and stop/start a process. These devices can be switches, sensors, pushbuttons or relays. A PLC control panel in it's simplest form is an enclosure that houses both the PLC and all other necessary components that are required to distribute low voltage power, carry out programmed outputs, and monitor the connected devices circuits.
Motor Control Centers: These are also called MCC's and are often installed in expansive manufacturing facilities that need to control numerous motors from a central location. The MCC usually houses the motor controls necessary for increasing speed, torque, or reversing the motor. Motor Control Centers make use of one or more vertical cabinet sections that have a common power distribution busbar and mounting locations. Often these are located at the main electrical service entrance of a building. One of the important components found in the motor control center is the filter or line reactor, another important device is the or motor starter, together with an overload relay this functions as protection for the motor. There are also circuit protection devices such as a circuit breaker, fuses, and a power disconnect switch. MCC panels also contain other control components such as variable frequency drives (VFDs), programmable logic controllers (PLCs), electrical metering devices, pushbuttons and indicator lights.
Power Distribution: Since main power, motor controls (like VFD's) and power switching devices (i.e. = contactors) generate electrical noise, the PDU cabinets are often separated or contained in another enclosure. Therefore, you end up with a lot of separate power distribution needs in a manufacturing environment. A typical power distribution panel is usually outfitted with a transformer to get to the proper voltage levels, usually stepping down 480V. A surge protection device to prevent overloading, and an AC/DC power source to supply the 24V DC devices (HMI and I/O). Other peripheral devices will include connectors, terminal blocks, power distributor modules and wires.
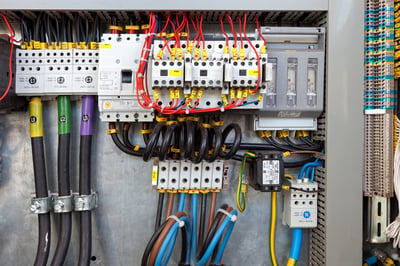
The Power Circuit: This is defined as any circuit that uses electricity to operate a load on the industrial control panel. Closing and breaking the circuit causes the machine to start or stop or the tell the machine to perform on/off power switching functions.
The Control Circuit: This type of circuit is used to manage all power circuits that are present on the panel. The control circuit also ensures safety from short circuit and harmonious machine control. These are extensively used to automate the machine and create safety for the human operators.
Important note: The power circuit and the control circuit both have switches that are used to control the starting and stopping of the machine connected to the industrial control panel, they are not the same and are often mistaken for one another. A circuit with two wires for the path, a switch for the control device and a motor for the load is a good illustration of what a power circuit is.
On the other hand, a control circuit is a special type of circuit used to control the operation of a completely separate power circuit.
Contact us to find out more about other control panel types, compositions and functions.
Now that you know the control panel types and how to Apply In your Project.
Let’s move onto the most essential thing in the control panel
the control components !
Just like the parts of your body work together to bring about it’s normal functioning, different components or parts of a control panel also need to work together. Marrying the proper components together determine the the overall design, operation and control of the machine or processes function. Below are some key components of the typical industrial control panel that you should familiarize yourself with.
Terminal Blocks: These are the modular and insulated blocks used to connect circuits to one another in the control panel. Terminal blocks function to increase safety and this is achieved by grounding, isolating, and protecting the other components in the electrical circuit. They are accessible with finger-safe connections to prevent electrical shock and can also provide test points, a feature that adds even more safety to the circuit.
Contactors: Often, in control panel design, relay circuitry is required for switching high current devices and this is where contractors come in. Unlike a circuit breaker, a contactor is not intended to interrupt a short circuit current. Contactors are electrically controlled switches that serve as the power relay circuitry needed to switch an electric load. They are able to make or break power to the device being controlled.
Transformers: The purpose of the transformer is to transfer electric power from the primary circuit to the secondary circuit. The transformer is a static device that either reduces (steps down) or increases (steps up) the voltage to match the requirements of the controls. The action involves using primary and secondary windings and results in power transfer via magnetic flux without changing the frequency.
Overcurrent Protection Devices: They are mainly a quick acting shield to protect the machines computer and sensitive electronic systems connected to the main from electric power surges. Overcurrent protection devices include circuit breakers and fuses, and are meant to protect against the potentially dangerous effects of overcurrent. Over currents can be caused an overload event (power surge) or a short-circuit current, which creates an electric fault. There are major differences in what can be used as main protection vs. branch circuit protection.
These are some of the more critical components which are essential for the electrical power within a control panel. The goal of such circuits is to control the process or equipment and provide a single collective base of operations where an employee/operator can manage the manufacturing process.
One final tip in regards to wiring your control components and the safety of your panel ... You must have an excellent earth to ground connection. Control panels have an incoming power feed with a grounded conductor, which needs to be bonded to the enclosure. This can be done via Ground Terminal Block, Ground Lug, Or Grounding Bus Bar if you do not have good ground contact this can lead to many problems later with either safety from electrocution or just hours of trouble shooting. When in doubt Ground It!
At Dynamic, we always stay up to date on innovations and new technology. The devices we represent are thoughtfully designed with consideration to the above-mentioned properties, and will improve your control equipment tasks. Are you looking to create a control panel or need industrial circuit design assistance for your concept? We love to improve machine control and design new systems!
We hope you found our information about the control panel useful. To further boost your knowledge of industrial control panel design, you can get additional info from other resources such as -> what makes a good control panel design. <- You can also stay in touch with us by signing up for our newsletter and receive updates when we have promotions or new blog posts.
If you need additional assistance please reach out to us to discuss your control panel component needs.