The fuel cell manufacturing process has become increasingly complex recently, with new technologies and processes continually being developed. Furthermore, as the fuel cell industry has grown, so has the demand for high-quality, efficient, and cost-effective manufacturing. In this blog post, we will explore the fuel cell manufacturing process and the different components that contribute to it.
The parts of a fuel cell are:
- The fuel cell stack.
- Fuel cell electrodes.
- Fuel cell membranes.
- Fuel cell separators.
- Fuel cell control systems.
Fuel cell stack: The fuel cell stack is the most critical component of the fuel cell manufacturing process, as it contains the fuel cell and its associated features. The fuel cell stack must be designed to meet the specific requirements of the fuel cell application.
Fuel cell electrodes: The fuel cell electrodes are responsible for transferring electrons between the fuel cell and the external circuit.
Fuel cell membranes: Located between the anode and cathode, the fuel cell membranes are responsible for separating the fuel and oxidant streams. They allow the proton to pass through but restrict the passage of electrons.
Fuel cell separators: The fuel cell separators are used to prevent mixing the two streams.
Fuel cell control system: The fuel cell control system is responsible for the efficient and safe operation of the fuel cell. The fuel cell control system includes microcontrollers, motor control systems, and other components. The microcontroller is used to monitor the fuel cell stack and control the fuel cell components, while the motor control system is used to manage the fuel cell pumps and valves.
Choosing the Right Materials for Fuel Cell Manufacturing
The selection of materials is a critical step in the fuel cell manufacturing process. The wrong material can lead to a decrease in performance or even failure of the fuel cell. When choosing the materials for the electrodes, the electrolyte, and the membrane, it is essential to consider factors such as cost, durability, and electrical conductivity. The material chosen for the electrodes must be able to withstand the high temperatures generated by the fuel cell and must be able to conduct electricity efficiently. The material selected for the electrolyte must be able to maintain its form and be able to transfer ions between the electrodes. Finally, the chosen material for the membrane must be able to separate the electrolyte from the electrodes while allowing ions to pass through.
In addition to the component materials, the construction materials of the fuel cell stack must also be considered. The fuel cell stack components include the cells, end plates, and connections. These components must withstand the high temperatures generated by the fuel cell and the pressure formed by the hydrogen and air mix in the fuel cell. The material chosen for the fuel cell stack must also be lightweight yet strong enough to support the weight of the fuel cells.
Design Considerations for Fuel Cell Manufacturing
In addition to the materials used, the fuel cell design is also an essential factor in the manufacturing process. The design must consider factors such as efficiency, durability, and cost. The type of membrane used must be able to separate the electrolyte from the electrodes while allowing ions to pass through. And ultimately, the design must also ensure that the fuel cell can generate enough power to be useful.
When designing the fuel cell, it is essential to consider the size and shape of the electrodes, the type of electrolyte used, and the type of membrane used. The size and shape of the electrodes must be optimized to maximize the efficiency of the fuel cell. The larger the surface area of the membrane electrode area, the more current it can produce. The more "stacks" in the cell, the more voltage it can produce. The type of electrolyte used must facilitate the flow of ions between the electrodes and, of course, be able to withstand the high temperatures generated by the fuel cell.
In addition to the design of the fuel cell, it is also essential to consider the layout of the fuel cell stack. The structure must be optimized to maximize the efficiency of the fuel cell and must also be able to support the weight of the fuel cells.
Pre-Assembly Checks for Fuel Cell Manufacturing
Before the fuel cell is assembled, it is vital to perform a series of checks to ensure that all components are in good condition. Such as, Checking the anode and cathode for any signs of damage and, additionally, the fuel source and oxidant for any signs of contamination.
It is also essential to check the electrolyte for any signs of contamination or leakage, as this can negatively impact the fuel cell's performance. Additionally, it is vital to ensure that all connections are secure and that the fuel cell is adequately sealed.
A step-by-step guide to the Fuel Cell Manufacturing Process
The manufacturing process for fuel cells involves several steps.
The first step in fuel cell manufacturing is to create the cell stack. The cell stack is comprised of individual fuel cell components stacked together, such as the membrane electrode assembly (MEA), separator plates, and gaskets. Each layer is carefully sealed together preventing any gas leakage.
The next step is to assemble the complete fuel cell stack. This involves connecting all the cells to form a single, integrated unit. Next, the cells are connected using special electrical connectors, which provide a path for the electricity generated by the fuel cell, ensuring that the fuel cell can safely and efficiently distribute the electricity.
The third step in fuel cell manufacturing is to test the stack to ensure that the stack is working correctly and that there are no issues with the fuel cell components. The testing process includes measuring the voltage and current output of the fuel cell, as well as checking for leaks.
The last step in fuel cell manufacturing is to package the fuel cell stack. This involves sealing the stack in a protective casing and attaching necessary safety features. The packaging also protects the fuel cell from damage during shipping and storage.
Below are some necessary components used in fuel cell manufacturing.
Microcontroller and Motor Control for Fuel Cell Manufacturing
The microcontroller is an essential component of the fuel cell control system, as it monitors the fuel cell stack and controls the fuel cell components. The microcontroller is typically programmed to monitor the fuel cell stack and provide feedback to the fuel cell control system. In addition, the fuel cell control system will controls the pumps and valves. Fuel cells can have a sophisticated motor control system. The motor control system is typically programmed to provide the necessary power to the fuel cell pumps and valves, as well as to monitor the fuel cell stack and provide feedback to control the overall fuel cell process. The motor control system can also be used to adjust the speed of the fuel cell pumps and valves.
Solenoid for Valve Control in Fuel Cell Manufacturing
The solenoid is an essential component of the fuel cell control system, as it controls the valves. The solenoid is typically programmed to open and close the fuel cell valves in response to the fuel cell stack's needs. The solenoid is also used to adjust the fuel cell valves' speed and provide feedback to the fuel cell control system.
The solenoid is typically used with the motor control system to ensure that the fuel cell valves operate efficiently and safely. The solenoid is also used to ensure that the fuel cell valves operate at the correct speed and that the fuel cell stack operates at the correct pressure.
Heat Dissipation Challenges in Fuel Cell Manufacturing
Heat dissipation is a major challenge in fuel cell manufacturing. The heating or cooling system must keep the fuel cell stack at a specific temperature to operate efficiently and safely. Heat dissipation is typically accomplished through radiators, fans, and other cooling systems to ensure that the fuel cell stack stays at an optimum working condition. To maintain the correct temperature, the control system must be programmed to monitor the fuel cell stack and adjust the cooling systems accordingly.
In addition, the fuel cell control system must be programmed to monitor and adjust the cooling systems when the temperature increases. Temperature control is crucial for fuel cells operating at high demand with increased temperatures, as the fuel cell stack may become damaged if the temperature is too high.
SSR and Contactors in Fuel Cell Manufacturing
Solid state relays (SSR) and contactors ensure that the fuel cell operates efficiently and safely. The SSR or contactor will control the opening and closing of electrical contacts that turn the fuel cell pumps and valves on and off. The SSR can also be programmed to monitor and control the heating or cooling of the fuel cell stack and provide feedback to the fuel cell control system. The SSR can also be used to adjust the speed of the fuel cell pumps, open and close valves, and monitor the voltage of the fuel cell.
DC/DC Converter and DC/AC Inverter
Fuel cells can produce very low DC voltage, but the voltage output is volatile and can change instantly. Traditionally when this type of power source is connected to a load, it becomes even more unstable and will experience a dramatic voltage drop. DC/DC converters can overcome the problem of varying voltage on the DC output. A DC/DC converter will provide a smooth constant voltage output and allow the fuel cell to drive an electrical load efficiently. Devices such as refrigerant and cooling systems may need external AC power to operate efficiently. In these cases, a DC/AC inverter can replace an external power source and drive the load that consumes alternating current directly from the fuel cell.
Sensors for monitoring, control, and measurement of the Fuel Cell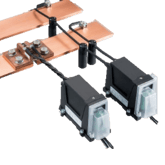
Sensors are essential to fuel cell manufacturing, as they monitor the fuel cell stack and control the fuel cell components. Sensors monitor the fuel cell stack and provide feedback to the control system.
The sensors are needed to monitor parameters such as pressure and temperature and measure the current and voltage. The sensors will also be necessary to monitor and adjust the fuel cell pumps' speed and determine the fuel cell's valve positions. A fuel cell could become very unsafe without these parameters being monitored.
Connectors for ease of manufacturing, testing, and use
The utilization of proper connectors is essential to fuel cell manufacturing. Adapters, couplings, and hose fittings will be necessary for the fuel, oxygen, and coolant lines.
A fuel cell typically requires several electrical connectors to connect the various components of the system too. Some common types of connectors used in fuel cell systems include High Current Connectors, Terminal Blocks, Sealed Circular Connectors, and possibly IEC Pin and Sleeve to connect the load.
Post-Assembly Checks for Fuel Cell Manufacturing
Once the fuel cell has been assembled, it is essential to perform a series of checks to ensure it is operating correctly. Running tests to ensure that the fuel cell produces the correct amount of electricity and functions efficiently is essential to safety.
It is also essential to check the fuel cell for any signs of wear or damage, as this can harm its performance. Additionally, it is necessary to ensure that all connections are secure and that the fuel cell is adequately sealed.
Quality Control in Fuel Cell Manufacturing
Quality control is integral to fuel cell manufacturing, ensuring that it operates efficiently and safely. Quality control is typically accomplished through quality assurance tests, ensuring that the fuel cell works at the correct temperature, voltage, and pressure.
In addition, quality control is also used to ensure that the fuel cell is free from defects and that the fuel cell components are functioning correctly. Quality control is accomplished through quality assurance tests, which ensure that the fuel cell operates at the correct temperature, voltage, and pressure.
Troubleshooting Fuel Cell Malfunctions
If the fuel cell is not operating as expected, an issue may need to be addressed. Identifying the cause of the problem and taking action to resolve it is essential. Typical fuel cell maintenance can involve replacing worn springs or damaged seals in the fuel cell itself.
If the issue is not related to the fuel cell, it may be related to the power supply or wiring. It is vital to ensure that all connections are secure and that the fuel cell is correctly connected to the power supply. If the issue persists, it may be necessary to seek professional help.
Challenges in Fuel Cell Manufacturing
The fuel cell manufacturing process is complex and requires the integration of several components, which can present several challenges. One of the significant challenges in fuel cell manufacturing is the integration of the fuel cell components, as this requires the integration of microcontrollers, motor control systems, solenoids, and other electrical components. Another challenge is integrating the fuel cell control system, which requires understanding the fuel cell stack function and its associated components.
In addition, heat dissipation is a major challenge in fuel cell manufacturing, and the fuel cell stack must be kept at a specific temperature to operate efficiently and safely. Finally, quality control is a significant challenge in fuel cell manufacturing. It is essential to ensure that the fuel cell is working properly and that its components are functioning correctly.
At Dynamic measurement & control solutions, we understand the complexities of the fuel cell manufacturing process and can provide you with the answers you need. In addition, our team of experts will work with you to create a plan that fits your needs and budget. So reach out to us; we can help you unlock the potential of fuel cell technology and create a more sustainable future.