High voltage electric and electronic devices are always vulnerable to electric arc. Electric Arc happens when current bridges the air gap between two conductors. A main source of this type of arc is when a high voltage circuit makes and breaks. Electric arcs can cause serious hazards if not extinguished in time. The biggest problem for switching current current is when you have a high current DC load and how do you turn off the arc which is generated when the switching contacts open.
There are ways to control electric arc, such as safety devices and over-current protectors. But, what about safely switching electrical power during operation in a circuit you need to control? Perhaps the safest and most effective device to open and close contacts is the electric contactor. Contactors come in a variety of types and specifications; some are designed specifically AC voltage or DC voltage and others are designed for both. The difference comes in their construction and the most difficult challenge is breaking the current in both directions (bidirectional).
AC Voltage
AC voltage has over one hundred zero-crossings every second, the current’s direction keeps changing, which means there are several times per second where the current is very low. The self-extinguishing nature of AC voltage lowers the risk of a dangerous electric arc in that AC power is much easier to control making switching AC much easier. The arc is self-extinguishing every time the waveform crosses zero which happens several times, depending on the AC frequency, while the contacts open and move apart.
Dc Voltage
DC voltage has no zero-crossings, therefore the current’s direction and intensity always remains the same. In a DC circuit there is not a “chance” of electric arc, it is inevitable! As the voltage increases so do the challenges and risks associated with breaking the DC circuit. These factors combined make it difficult to regulate electric arc when DC voltage makes and breaks. For a DC load, the only way to turn the switching arc off is to have a contact gap big enough that the arc eventually "blows itself out". This requires a large amount of air space to do the switching (big gaps require distance and therefore big coils to move contacts long distances). A number of techniques have been developed to safely extinguish the DC switching arc. One of the earliest ideas was to use a magnet to extend the arc distance (or “blow out” the arc). The use of fixed magnets or electro-magnets has been proven to steer the arc in a direction of choice and still the most popular electro-mechanical method in use today. The use of an electro-mechanical blow out technique that utilizes magnets aloows for smaller sized DC relays and contactors than would otherwise would be possible.But the situation is more challenging in DC power.
Using an intelligently designed DC Contactor is the only way electric arcs can be extinguished safely in an off (opening contacts under load) switching circuit.
There are different types of electrical phenomenon in DC circuits, Resistive, Capacitive, and Inductive. So, what type of contactor is right for your design?
Let’s take a look at the differences and what they mean for the two primary types of DC Contactors.
Electromagnetic Blowout Contactors Vs. Gas-filled Contactors; What is the Difference?
Both types of DC contactors utilize a DC electromagnetic coupling to open and close the contacts. The arcing effect of breaking the DC load are increased temperature, melting, and burning ... none of which are good for electrical contacts. Hermetically sealed gas-filled contactors use an inert gas to minimize and extinguish the arc whereas the environmentally balanced type (blowout chambers to exhaust the arc) or electro-mechanical blowout contactors use an electromagnet and a directed arc chute to stretch and “blowout” the arc.
The primary difference between both types is that gas-filled contactors contain a mixture of nitrogen, hydrogen or SF6 gas hermetically sealed in a contact chamber which moves the arc, cools it off, and extinguishes it to protect a copper contact. Whereas the environmentally balanced, electromagnetic contactors, elongate, cool, and extinguish the arc through the electromagnetic blowout field. This is done by creating strong magnetic field that directs the arc away from the contacts and pushes it into a thoughtfully designed arc chute. This happens very quickly which keeps the contacts cool this also allows for a harder finishing material and larger contact to minimize the pitting and burning of the contacts. The electromagnetic device can be designed in such a way the contacts will last longer in high current and high voltage applications.
Short-Circuit Capacity
In the event of a short circuit the rising current generates a repulsion or levitation force working against the contacts desired opened or closed operation (Coulombs Law). If this exceeds the holding force of the contacts you will, at minimum, have heavy arcing and temperature build up causing the contacts to weld together. Electromagnetic blowout contactors are more robust and prevent welding of the contacts because of the short circuit ratings. The reason for the high short-circuit capacity is because of the high contact forces they maintain in open air as opposed to under vacuum. This also reduces contact bounce which damages contacts even further. Whereas gas-filled contactors cannot withstand short-circuits for equally long durations and therefore have lower inrush and short circuit ratings, especially when “making” contact. Many of them are also limited to unidirectional current flow, which can also be problematic.
Thermal Characteristics
Gas-filled contacts easily heat up as they have nowhere for that heat to go, especially after repeated operations. An electromagnetic blowout contactor with open venting does not have this issue. Furthermore, because gas filled contactors are sealed, they have the potential for overpressure. In high over-current events or if they do experience a short-circuit this generates excess gas pressure inside the contact chamber, which could lead to an explosion. However, the electromagnetic contactors are deemed safer as they do not have a sealed contact chamber. In general, the external forces created in a sealed environment are much greater than the ones with free air exchange that allow pressure to escape the device.
Applications of Electromagnetic Blowout and environmentally sealed Contactors
Most environmentally balanced electromagnetic contactors support bi-directional current flow at full capacity when the blowout is designed properly. The gas filled device are not bidirectional and cannot break or "turn off" current successfully over many operations. Since electromagnetic blowout contactors can regulate bidirectional DC power as high as 4.8 kV and 2000 A, they are feasible for controlling high-power DC equipment. Electromagnetic blowout contactors are commonly used in the following industries.
EV and EVSE
Electric vehicles charge and run-on high DC power. With today’s superpowered EV’s they generate up to 250kW which is more than high enough to generate arcs. Therefore, electromagnetic blowout contactors are used in electric vehicles to safely switch on and off the high voltage current flow used in battery switching applications. The EV charging infrastructure and Level 3 DC fast chargers are also using high-voltage DC with large levels of current, moving to 200kW and above! To speed up battery charging, well designed DC contactors are very much needed to safely shutoff and break current loads.
Power and Energy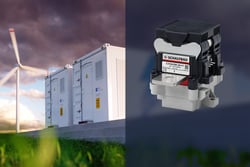
Renewable-based power generation inverters input high DC power. Applications such as Solar and Wind Power use electromagnetic contactors for safe switching. You will find the need to break the DC loads during the inverter process as well as when moving stored energy to and from the batteries.
Manufacturing and Industry
Facilities continue to evolve towards using more DC energy, whether it is an energy storage or backup system, UAV or fleet management, or even to charge forklifts. You will find more DC contactors as facilities continue to automate their high-power DC equipment, especially motors. Just switching motors on and off can produce electric arc. Other heavy DC electric burdens can be found in applications for Light Rail, Marine Electrical Systems, Aircrafts, Battery Manufacturing and Test Equipment. Huge overpressures are always generated by an upcoming DC arc. In critical environments to ensure a safe switch off procedure, a vented, but environmentally sealed contactor reduces the risk of a thermal event or explosion.
Key Takeaway: Environmentaly Balanced Electromagnetic Blowout Contactors can be Very Effective
Electromagnetic blowout contactors help maintain a safe environment. In certain applications vented electromagnetic contactors have an edge over their gas gas-filled counterparts. Key advantages of a vented electromagnetic blowout type contactors would be in the event of high thermal limits, applications needing high contact force (risk of levitation), risk of gas leakage, risk of overpressure or explosion, and materials of the contacts last longer. Moreover, the electromagnetic blowout type will withstand short-circuits better than gas-filled contactors. The higher the DC current and voltage levels and the more emphasis needed on safety or life critical applications, the more the electromagnetic blowout contactor will become suitable for the application.
If you want to discuss this topic in more detail or need some additional information, send the application engineers at Dynamic an e-mail!