PID control is widely used to control industrial processes. It is a feedback control system that uses sensors to measure the output of a process and adjusts the input to keep the process at a desired set point. In this blog, we will discuss in detail whether AI will replace PID control.
What is PID control?
The PID controller or Proportional-Integral-Derivative control calculates an error signal, which is the difference between the set point and the actual process output, and then adjusts the input to the process based on that error signal. The Proportional term adjusts the input in proportion to the error, the Integral term adjusts the input based on the accumulated error over time, and the Derivative term adjusts the input based on the rate of change of the error signal.
Advantages and limitations of PID control
PID control is a popular control method because of its simplicity and reliability. It is easy to implement and can be used for many processes. It is also a robust control method that can handle disturbances and changes in the process.
However, there are some limitations to PID control. It requires tuning the control parameters for each specific process, which can be time-consuming and challenging. PID control also assumes a linear relationship between the process input and output, which may not always be accurate. Additionally, PID control does not adapt to changes in the process over time.
The evolution of PID control
PID control has been around for over a century, and over the years, it has become more sophisticated. Elmer Sperry invented the first PID controller in 1911 to control the steering of ships. Since then, PID control has been used in various applications, from heating and cooling systems to robotics and automation.
In recent years, there have been advancements in PID control, such as fuzzy logic and neural networks. These methods can improve the performance of PID control by adapting to changes in the process and reducing the need for manual tuning.
AI and machine learning in PID control
- The world of control systems has significantly transformed by incorporating Artificial Intelligence (AI) and Machine Learning (ML) techniques. One of the most promising applications of AI and ML is in the field of PID control. PID control is a widely used technique to maintain a desired output value by adjusting the input value based on feedback. It is a closed-loop control system used in various industries, such as manufacturing, robotics, and aerospace.
- Integrating AI and ML in PID control systems has resulted in more efficient and accurate control. With the help of AI, controllers can automatically adjust the PID parameters based on the changing conditions, resulting in improved performance and reduced error. In addition, machine Learning techniques can be used to train the controller to learn from past data and predict future behavior, making the control system more adaptive and responsive to changes.
- Furthermore, AI and ML techniques can also optimize the PID controller's performance. Optimization algorithms can be used to find the best set of PID parameters that result in the most efficient control. This optimization can be done in real-time, resulting in better control performance and reduced energy consumption.
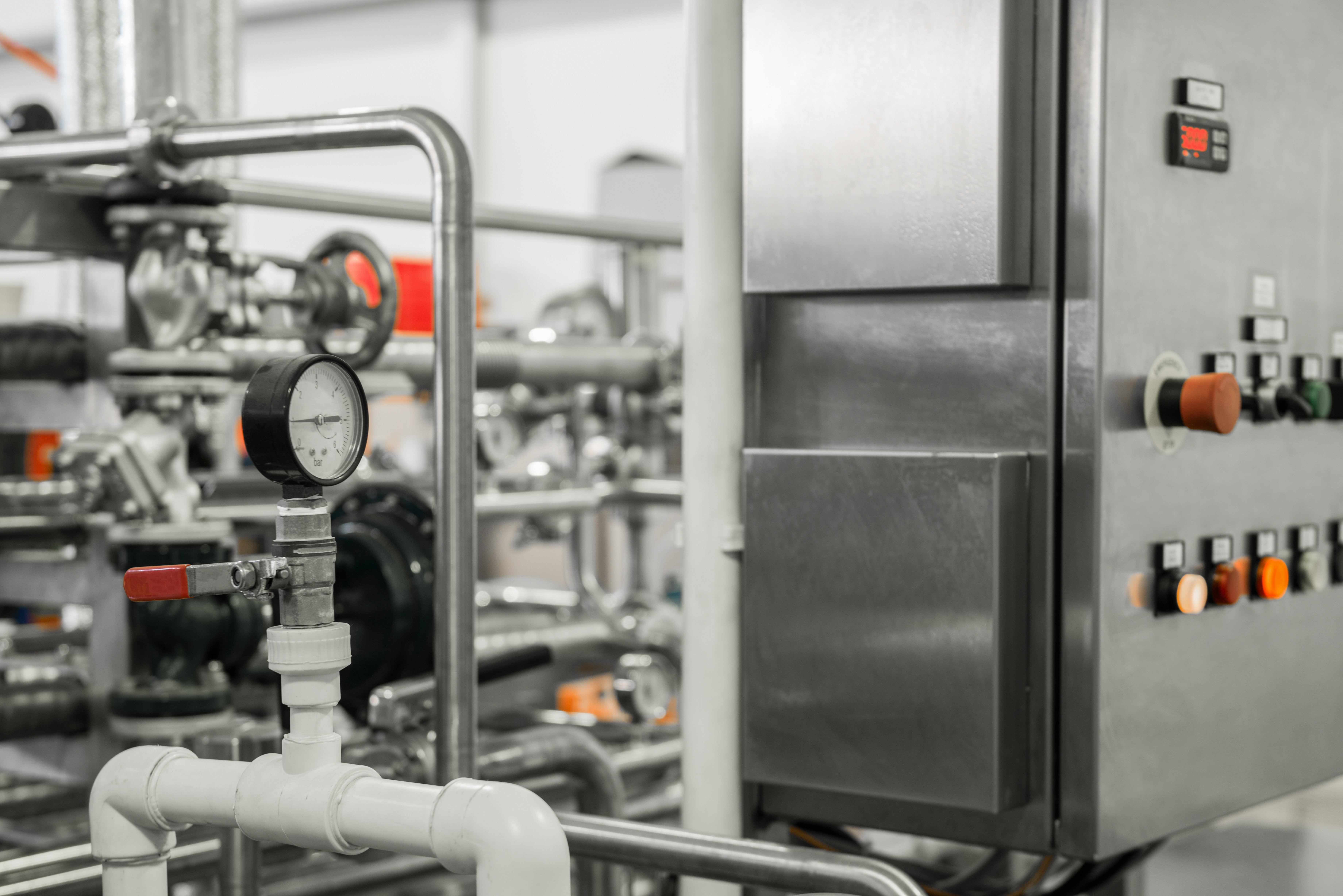
Advantages and challenges of AI in PID control
- The use of AI in PID control has many advantages. Artificial Intelligence (AI) is an advanced technology that has revolutionized many industries, including control engineering. One of the most significant applications of AI in control engineering is in Proportional-Integral-Derivative (PID) control. PID is a widely used control algorithm that regulates a process by adjusting the control variables based on error feedback. Integrating AI with PID control can significantly enhance the system's performance, making it more efficient and effective.
- One of the primary advantages of AI in PID control is its ability to learn from data and adapt to changing conditions. AI algorithms can analyze large amounts of data, identify patterns, and predict the system's behavior. As a result, an AI component can optimize the control variables and ensure that the system operates at peak efficiency. Additionally, AI can reduce the system's complexity by automating specific processes, thus improving the overall control performance.
- However, there are also some challenges associated with the use of AI in PID control. One of the most significant challenges is the need for large amounts of data to train AI algorithms. This data must accurately represent the system's behavior to ensure that the AI can learn effectively. Another challenge is the need for specialized skills to develop and maintain AI algorithms. This can be a significant barrier for small organizations needing more resources to hire AI experts.
Case studies of AI in PID control
Several case studies have highlighted the potential of AI in PID control. For example, one study explored using a neural network-based PID controller for a heating and ventilation system in a commercial building. The AI-driven controller improved energy efficiency by up to 20% by leveraging real-time data from temperature and humidity sensors. Another study focused on a water treatment plant, where an AI-based PID controller could reduce chemical consumption by 15% while maintaining water quality within desired parameters.
AI can also optimize PID control in complex systems such as those in the manufacturing industry. For example, in one case study, an AI-based PID controller was used to regulate the temperature of a glass furnace, resulting in a 50% reduction in energy consumption and improved product quality. Similarly, an AI-driven PID controller was used to regulate a chemical processing plant's pressure and flow rate, resulting in a 30% reduction in operating costs.
PID control vs. AI: Which is better?
The question of whether PID control or AI is better for controlling industrial processes is a complex one. Both methods have advantages and disadvantages; the best approach depends on the specific application.
PID control is a classic method used for many years in control systems. It is a simple and effective method that adjusts the control output based on the error between the desired setpoint and the actual process variable. The proportional, integral, and derivative terms are used to adjust the control output based on the error, the error rate of change, and the error's integral over time, respectively.
On the other hand, AI is a more robust and complex method that uses machine learning algorithms to optimize the control output. In addition, AI can learn the system's behavior and predict future behavior, allowing it to make more accurate and precise control decisions.
In terms of performance, AI has the potential to outperform PID control, especially in complex and dynamic systems. However, AI requires a large amount of data to train the machine learning algorithms and can be challenging to implement and maintain.
In short, choosing between PID control and AI depends on the specific application and requirements of the control system. For simple designs, PID control may be sufficient. However, AI may be the better choice for complex and dynamic systems. Ultimately, it is up to the control engineer to decide which method to use based on their expertise and knowledge of the system.
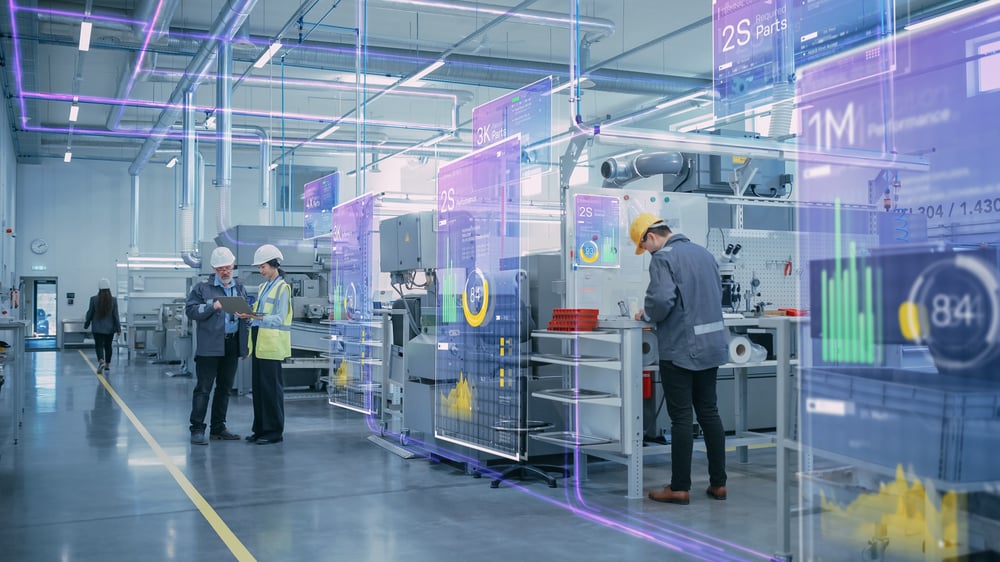
The future of PID control with AI
The future of PID control with AI is promising. As AI technology advances, more industries will likely adopt AI in their control systems. In addition, AI can improve the control system's performance by adapting to changes in the process and predicting future behavior.
However, it is unlikely that AI will only partially replace PID control. PID control will continue to be used in many applications where simplicity and reliability are essential. Instead, AI will augment PID control, improving its performance and reducing the need for manual tuning.
Expert opinions on the future of PID control
Experts in control systems have different opinions on the future of PID control with AI. Some believe that AI will eventually replace PID control, while others believe that PID control will continue to be used in many applications.
One thing is clear, however – the use of AI in control systems will only become more prevalent in the coming years. As AI technology improves, it will become more accessible and easier to use, making it a valuable tool for controlling industrial processes.